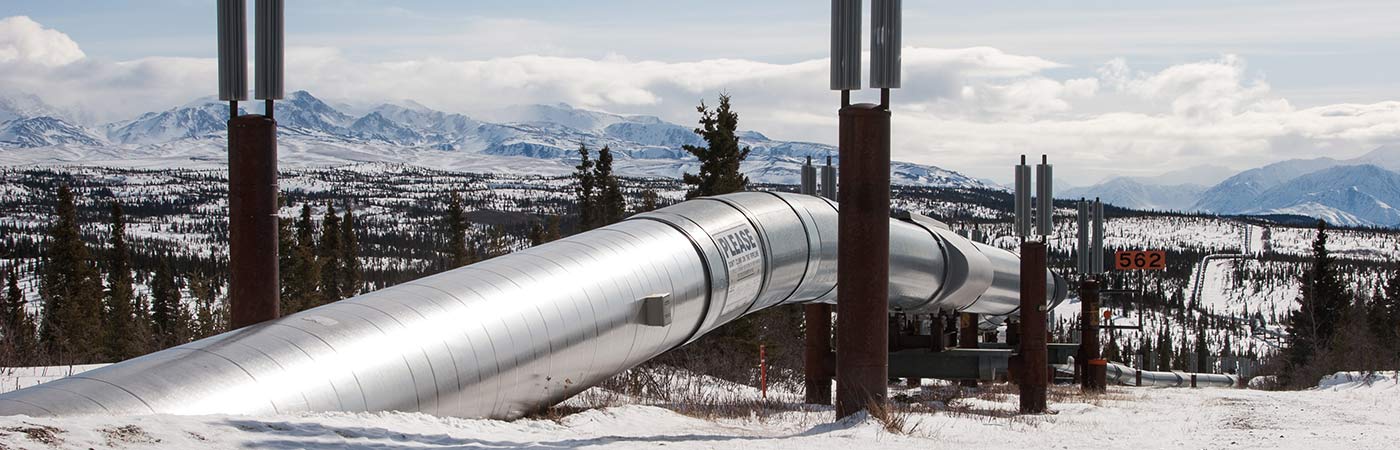
Advanced materials
Research and innovation in advanced materials at The University of Manchester focuses on solving some of the world’s most critical problems.
We need metals that can survive in the harshest conditions, enabling us to dig at deeper ocean depths or to transport the fuels of tomorrow. As the world becomes more connected we need to travel more often and at greater speeds.
To do this we’ll need stronger, lighter materials.
What's your area of interest? Choose from the below categories.
At the forefront of advanced materials
Manchester is a world leader in developing new and existing materials for extreme environments. We also lead the world in the characterisation of materials – measuring and exploring materials that will help us fully understand their properties and potential. Manchester is also at the forefront of biomedical materials, as well as new materials designed to serve the nuclear energy sector.
Our reputation is reinforced by vast capital and research investment, with more than £248m of live research projects. The University of Manchester will be the home of the £235m Henry Royce Institute, supported by partner universities, which will play a crucial role in addressing the challenges facing society and making advanced materials a catalyst for economic growth in the UK.
In all of our advanced materials research, we are working with dozens of industrial partners to bring discoveries from the lab to the lives of real people. We host the £64m BP International Centre for Advanced Materials which has established the University as a leading hub for advanced materials expertise, working in collaboration with some of the finest researchers across the world to further the understanding and use of materials in the energy sector.
Materials of the future
And then there’s graphene. One-atom thick, this material is set to revolutionise the material world.
Our team of more than 200 graphene and related two-dimensional materials researchers are constantly coming up with new ways to improve and transform current products, from providing clean water for millions in developing communities to creating sustainable energy storage devices.
Manchester’s world-class status as not only the birthplace of graphene but also the centre of its international commercialisation has been reinforced by more than £120m of capital funding to establish the National Graphene Institute and the Graphene Engineering Innovation Centre.
These centres of excellence, along with the University’s ambitious new engineering campus and the Manchester-based Henry Royce Institute, will contribute to the exciting vision of Graphene City – a community of leading 2D materials scientists and engineers that will itself become a worldwide beacon, attracting investment and innovators from around the globe.
At The University of Manchester, we’re committed to advancing how materials work for the world. We’re revolutionising applications for society and industry, and finding solutions to some of the planet’s most challenging problems.
Advanced materials: Research breakthroughs
Safer aero engines
Developing aerospace engines with increased performance and safety standards.
Affordable desalination
Bringing fresh, clean, affordable drinking water to the developing world.
Global challenges, Manchester solutions
Clean drinking water for millions
Global challenge
Globally, up to 435 million people are taking water from unprotected wells and springs and by 2025 half of the world’s population will be living in water-stressed areas. The challenge is to provide safer, accessible and more reliable supplies of clean water.
Manchester solution
Graphene-based membranes have been described as the perfect barrier. They’re capable of separating two liquids to an exceptional degree and can block even the smallest atom, helium, from passing through.
Manchester research will enable future filtration systems to precisely control water permeation – from ultrafast permeation to complete blocking.
Graphene trainers that keep on running
Global challenge
Outdoor runners need footwear that combines heavy-duty grip and wear with lightweight construction. Manufacturers have long competed to find a solution to the demands of customers and the terrain.
Manchester solution
Dr Aravind Vijayaraghavan and his team at Manchester worked with UK running brand inov-8 to produce the world’s first range of sports footwear featuring graphene. The 2D material has been used to develop outsole rubbers that are scientifically proven to be 50% stronger, 50% more elastic and 50% harder wearing.
Biomedical materials that rebuild our bodies
Global challenge
Injuries or disease can leave people with significant and lasting physical impediments to daily life, effecting their long-term health and mobility. A priority challenge for biomaterials researchers is restoring biological function with minimum invasiveness.
Manchester solution
New medical approaches to improve human health and well-being are essential for maintaining the UK’s global position in medical technology. Professor Sarah Cartmell and her team at Manchester are developing biomaterials systems to help patients replace damaged or missing biological structures, essential for their health and mobility. By creating a biodegradable device called a scaffold they can guide tissue regeneration, such as a bone piece or layers of cartilage.
Revolutionising the manufacture of next-gen cars and planes
Global challenge
Growing populations and climate change are challenging vehicle manufacturers to find, sustainable solutions to our travel needs. They increasingly need new processes to produce lighter, cheaper and more adaptable materials.
Manchester solution
Cygnet Texkimp, a leading machinery manufacturer for the global aerospace and automotive sectors, teamed up with Manchester robotics and textile composite specialists to find a way to create complex components cost-effectively, in high volumes, and at high speeds. Building on a concept developed by Professor Prasad Potluri, the partnership produced the world’s first robotic 3D-winding machine, which could revolutionise manufacturing of next-generation cars and planes.
Rethinking our relationship with plastic
Global challenge
Plastic waste is a global problem. It’s estimated that 40 billion tons of plastic waste will be in the Earth’s system by 2050.
Manchester solution
Professor Michael Shaver heads a new Manchester-based initiative called RE3 – Rethinking Resources and Recycling – which is working with industry and academic partners to address technological and societal issues around plastic. His vision is to tackle the plastic challenge with breakthroughs in materials science and collective social responsibility.
Preventing corrosion
Global challenge
Globally, corrosion costs more than $2.5 trillion a year. Despite this large economic impact, the fundamental processes of corrosion are poorly understood and industry relies on field experience for its management.
Manchester solution
Researchers led by Dr Brian Connolly at the BP International Centre for Advanced Materials, based at Manchester, are working collaboratively to understand the fundamental processes that initiate corrosion. This research will lead to the development of improved strategies to prevent corrosion and ultimately increase the reliability and lifespan of pipelines in the oil and gas industry.
Developing the materials of the future
Global challenge
Advanced materials could help solve some of the world’s most critical problems, but we need to accelerate the discovery and development of new materials systems to bring economic and societal benefit to the UK.
Manchester solution
Manchester has a strong tradition of stimulating economic growth and industrial innovation. We’re home to the Henry Royce Institute, the UK’s national institute for advanced materials research and innovation, bringing together the brightest minds from across the UK, including world experts from the universities of Sheffield, Leeds, Liverpool, Cambridge, Oxford and Imperial, as well as the National Nuclear Laboratory and the UK Atomic Energy Authority.
Accident-tolerant nuclear fuel
Global challenge
The accident at the Fukushima Daiichi nuclear reactor in 2011 highlighted a challenge with the zirconium alloy used to make fuel rods. At the very high temperatures generated when coolant is lost, this particular alloy reacts with steam to produce explosive hydrogen gas.
Manchester solution
Researchers at Manchester’s Dalton Nuclear Institute are developing fuel solutions that are much more tolerant to prolonged excessive temperatures. Our Zirconium Group is leading MIDAS, a large project, funded by the Engineering and Physical Sciences Research Council, to increase understanding of the metal, enabling its safe use as a primary cladding material in nuclear reactor systems.
In-depth insight
Get an in-depth insight into some of our world-changing advanced materials research.
Read more
Experts for media
Our advanced materials experts can offer fresh perspectives and explain how we're advancing knowledge for a better world.
Read more
Faculty of Science and Engineering
Find out more about the sciences and engineering research carried out at the University.
Visit the Faculty of Science and Engineering website
Research beacons breakthrough ebook
Read our ebook for insights into how Manchester commercialises its world-class academic research.
Download our breakthrough ebook
Sustainable Futures
Find out how we're delivering solutions to urgent environmental challenges.
Read more
Sustainable Materials Innovation Hub
Helping businesses in Greater Manchester create sustainable solutions for plastics use.
Read more
Events
-
AMBS Event: A multi-level analysis of net-zero transitions Acceleration and new obstacles
1 May 2024, 12pm-1pm
At this Original Thinking Lecture, Frank Geels, Eddie Davies Professor of Sustainability Transition, will give his inaugural lecture as Eddie Davies Chair. Net-zero transitions hav.. -
A Community Event on Teamwork in Research
14 May 2024, 12pm-2.30pm
Hosted by The Team Research Programme, funded by Research England, who aim to increase awareness of the Team Research (Team Science) interdisciplinary model and its value to resear..