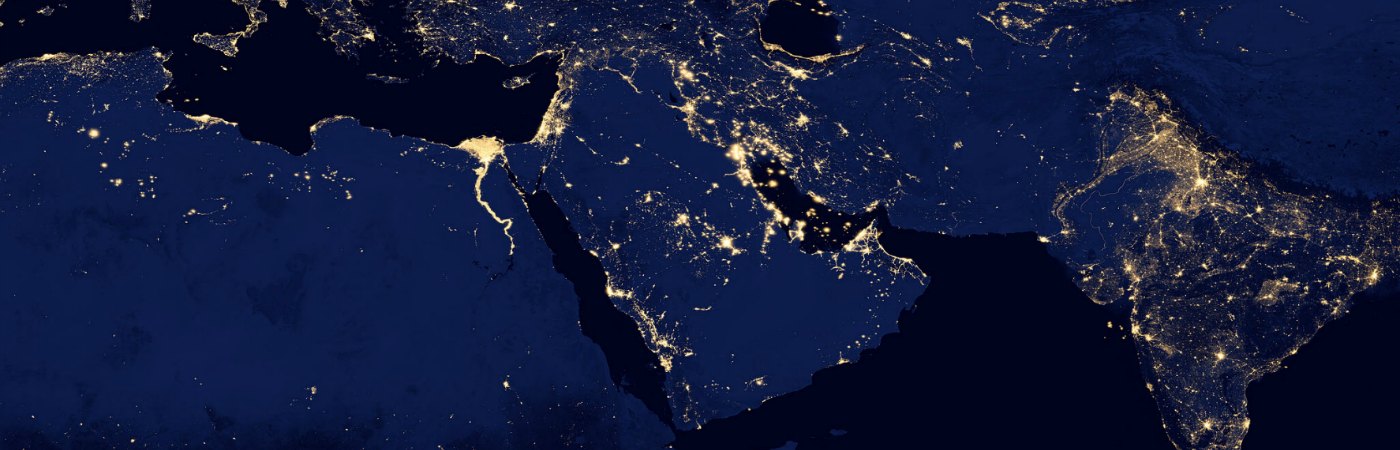
Research impact
The University of Manchester’s research delivers economic, environmental, social, cultural, health and wellbeing benefits across the globe.
We use our research expertise and pioneering spirit to discover, develop and create innovative solutions to the world's biggest problems and transform lives.
Driving invention and innovation
We work with government, business and not-for-profit organisations to deliver impact through innovation and commercialisation, including:
- Our internationally-leading role in graphene and 2D materials, supported through the National Graphene Institute and Graphene Engineering and Innovation Centre.
- Putting academic and student inventors’ ideas to work through our Innovation Factory, reinforcing our presence as a top university for invention.
- Driving digital transformation through our Digital Futures network of more than 1,700 researchers.
Transforming local communities
Our health research delivers benefits within the context of Greater Manchester’s devolved health and social care budget through partnerships with the NHS Trusts in Health Innovation Manchester and the Manchester Academic Health Science Centre.
The research and innovation strengths of our partnerships were brought together in an unprecedented way to form the COVID-19 research rapid response group to help address the public health crisis.
We also help Manchester’s arts, culture and creative industries thrive through Creative Manchester.
Fighting climate change
We're committed to research that improves the environment.
Our research into climate change has led to climate adaptation strategies being put in place across Europe, with our Sustainable Futures platform producing innovative solutions to urgent environmental challenges.
Global impact
We use our research to positively impact communities, such as:
- Our policy engagement institute, Policy@Manchester, uses research-informed evidence and ideas to influence and challenge policymakers.
- Ensuring public engagement, civic engagement, and cultural engagement are all core parts of our social responsibility plan.
- KEF results, where we are sector-leading for public and community engagement and research partnerships.
For health, equality and sustainability
Learn how our research is creating a healthier, fairer and greener world.
Research impact showcase
Learn how we're solving the world's most urgent problems.