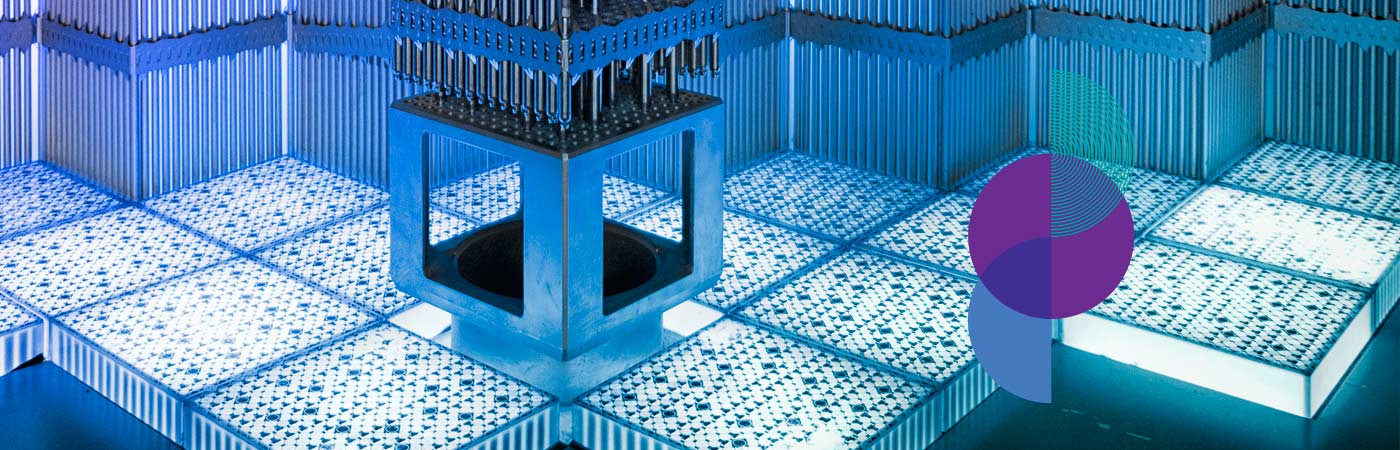
Energy generation – reactors and fuels
At Manchester we're bridging the energy gap.
The University of Manchester's Dalton Nuclear Institute has some of the most advanced research facilities in the UK and many internationally recognised researchers. Our work supports the UK nuclear industry in the operation, maintenance, management and life extension of existing nuclear reactors, as well as in the development of new manufacturing techniques for new nuclear build and the next generation of reactors.
The new nuclear build at Hinkley Point C, the UK’s first new nuclear power station to be built since 1995, increases the imperative to develop skills and deliver innovation.
Improving nuclear manufacturing
Our New Nuclear Manufacturing (NNUMAN) programme is the focus for nuclear manufacturing at Manchester. NNUMAN is providing industry with research and development to drive early-stage innovation in manufacturing.
The programme has four key themes: joining/welding, new approaches to machining, near-net shape manufacturing, and understanding and modelling the in-service performance of materials and components. Work covers major structural components, as well as nuclear fuel.
The most promising manufacturing processes delivered by our NNUMAN team will be taken forward to prototype by the Nuclear Advanced Manufacturing Research Centre (Nuclear AMRC) and, for fuel, the National Nuclear Laboratory (NNL).
The programme is intended to accelerate UK manufacturing companies’ access to new and more efficient technologies and methods, for greater cost effectiveness and competitiveness in the global nuclear industry.
The world works better with us.
Our Centre for Nuclear Energy Technology (C-NET) is supporting the continued operation of existing nuclear power plants, the design and deployment of Generation III and IV power stations, and the enhancement of fuel performance. Incorporating the new Nuclear Fuel Centre of Excellence (NFCE), C-NET is a driving force in meeting the national nuclear R&D programme needs in nuclear fuel fabrication and development.
We are developing and applying new technologies and methods. The world works better with us.
Manchester researchers in the EPSRC-funded NNUMAN programme are helping to improve welding and joining technologies for the next generation of nuclear power plants.
Our experts are working to make conventional welding technologies more efficient, and exploring novel techniques (such as electron beam, laser and hybrid laser-arc welding) to fabricate welds more quickly and reliably without adversely affecting their long-term performance.
We simulate the welding process by developing and validating advanced modelling techniques that predict how these welds will behave in high-pressure, high-temperature reactor environments. By understanding the potential degradation mechanisms that affect welds under these conditions, we can predict the future performance of these welds after decades of service, which is vital for safely extending the operating lifetime of the existing fleet of nuclear reactors, for new nuclear build and the design of future Generation IV reactors.
At Manchester we have the facilities and the expertise to study all of the different facets of welds and their behaviour – including dedicated welding facilities in our Manufacturing Technology Research Laboratory, Materials Performance Centre and Modelling and Simulation Centre.
We also benefit from working closely with industrial partners such as AMEC, AREVA, EDF, Hitachi GE and Rolls-Royce, as well as with the Nuclear Advanced Manufacturing Research Centre, collaborating on technologies as they are being commercialised.
“We will learn what is necessary for industry to make informed decisions about the choice of welding process, so that if they think about using laser or narrow-groove arc welding they understand the implications in terms of the performance of the nuclear components throughout their life: it is about relating manufacturing choices to through-life performance.” - Dr John Francis, Senior Lecturer in Welding Technology
“The target for applied research means that, although we need a high level of foundation knowledge and an understanding of the research, finally we have to deliver something very practical for industry use.”
Zunmin Geng, researcher
We advance understanding of how welds perform, for existing and next-generation reactors. The world works better with us.
By producing parts that are closer to their final shape, manufacturers can significantly reduce material waste, cost and lead times.
Components such as reactor vessel nozzles and valve bodies are usually machined down from forgings or billets. Our NNUMAN team are testing ‘near-net’ production processes for nuclear applications. These reduce energy consumption and material wastage by using techniques such as HIP – Hot Isostatic Pressing (advanced powder metallurgy originally developed for the aerospace industry) and additive manufacturing (carefully depositing layers of molten metal to create 3D shapes), thereby reducing the need for machining.
Our work also extends to the fabrication of specialist ceramic and coated materials required for advanced nuclear fuels.
We develop innovative technologies and also apply those first developed in other industries to nuclear energy, building a deep level of understanding of their potential through-life performance. The world works better with us.
By testing in conditions as close as possible to the real-world environment inside reactors, we can develop an understanding of how components in nuclear reactors will behave during long-term service.
The high-pressure, high-temperature environment within nuclear reactors is uniquely difficult to recreate. At Manchester we have the expertise to test materials in a range of reactor environments – including PWR, AGR, ABWR and some Generation IV reactors – and unique facilities that enable us to observe the specimens in situ. We also simulate radiation environments at our Dalton Cumbrian Facility.
These tests, combined with modelling work, are critical to understanding how new technologies and techniques (such as new welding and joining techniques) will improve component performance during service for several decades.
One example of our innovation in environmental testing is our use of Digital Image Correlation (DIC) to understand how cracks develop. Manufacturing nuclear components demands the highest level of integrity and assured reliability. We use such innovative techniques for assessing and predicting structural integrity. As part of a consortium with Imetrum and Rolls-Royce our researchers are working to assess the application of DIC as a means of assuring structural integrity in the manufacturing process.
DIC could enable the monitoring of the components in service and detect in-service creep, creep fatigue and environmental-assisted cracking. Positive initial results in a feasibility study, funded by the Technology Strategy Board, are encouraging, and leading to potential application in the remote detection of component ageing and the development of defects.
The fundamental testing and modelling of component manufacture and performance helps to ensure the future of the nuclear industry is secure. The world works better with us.
There are 14 advanced gas-cooled reactors (AGRs) in the UK. Our fundamental research underpins safe plant life extension supporting continued operation beyond original design lifetime.
AGRs provide a significant portion of the country’s nuclear electricity (typically 15%). Nuclear graphite is used as a moderator in these reactors, and in the UK’s one remaining Magnox reactor, but is considered to be a limiting factor in the AGRs’ operational life. The graphite ages and degrades with time, and therefore a thorough understanding of nuclear graphite’s mechanical and structural properties is important for safe life extension of existing reactors.
Our Dalton Nuclear Institute provides critical research and expertise to advise on the continued safe operation of the UK’s AGRs. Since 2001 our team of graphite experts has been an essential source of independent advice in the review of safety cases for consideration by the Office for Nuclear Regulation (ONR) – responsible for granting the licence for continued operation – enabling lifetime extension proposals for EDF Energy.
By providing critical research and advice, our experts work with the ONR and EDF Energy to deliver the reassurance needed for the continued operation of AGRs, so they can continue to generate power while new reactors are being developed. The world works better with us.